Unwinding the Secret of Porosity in Welding: Tips for Reducing Issues and Making Best Use Of Quality
In the complex globe of welding, porosity continues to be a relentless challenge that can significantly impact the high quality and integrity of bonded joints. As we dig into the midsts of porosity in welding, revealing the keys to its prevention and control will be paramount for experts looking for to understand the art of top quality weldments.
Understanding Porosity in Welding
Porosity in welding, an usual problem experienced by welders, describes the existence of gas pockets or gaps in the welded product, which can endanger the stability and top quality of the weld. These gas pockets are usually trapped during the welding process due to numerous variables such as incorrect securing gas, polluted base materials, or inaccurate welding specifications. The development of porosity can damage the weld, making it at risk to breaking and rust, ultimately bring about structural failings.
By identifying the importance of maintaining appropriate gas securing, making sure the sanitation of base materials, and enhancing welding setups, welders can dramatically reduce the likelihood of porosity formation. On the whole, a comprehensive understanding of porosity in welding is important for welders to generate high-quality and long lasting welds.

Common Root Causes Of Porosity
When examining welding procedures for prospective high quality concerns, recognizing the common reasons of porosity is vital for maintaining weld honesty and stopping structural failings. Porosity, identified by the existence of cavities or spaces in the weld steel, can substantially jeopardize the mechanical buildings of a bonded joint.
An additional prevalent root cause of porosity is the presence of moisture and pollutants on the surface area of the base steel or filler product. When welding products are not appropriately cleaned up or are revealed to high degrees of humidity, the evaporation of these impurities during welding can create spaces within the weld bead. In addition, welding at inappropriate parameters, such as excessively high traveling speeds or currents, can generate too much disturbance in the weld swimming pool, trapping gases and triggering porosity. By attending to these common reasons through proper gas shielding, product preparation, and adherence to optimal welding parameters, welders can reduce porosity and enhance the high quality of their welds.
Strategies for Porosity Avoidance
Applying reliable preventative procedures is critical in reducing the event of porosity in welding processes. One method for porosity avoidance is ensuring appropriate cleansing of the base steel prior to welding. Impurities such as oil, oil, rust, and paint can cause porosity, so detailed cleaning using proper solvents or mechanical methods is important.

One more key safety net is the option of the ideal welding consumables. Utilizing top notch filler materials and protecting gases that are suitable for the base steel and welding procedure can substantially lower the danger of porosity. Furthermore, maintaining appropriate welding parameters, such as voltage, existing, travel rate, and gas circulation price, is crucial for porosity prevention. Deviating from the advised setups can cause inappropriate gas coverage and inadequate fusion, bring about porosity.
Additionally, employing correct welding methods, such as maintaining a regular travel rate, electrode angle, and arc length, can aid avoid porosity (What is Porosity). Sufficient training of welders to guarantee they comply with finest techniques and quality assurance procedures is additionally important in decreasing porosity issues in welding
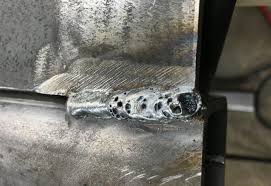
Ideal Practices for High Quality Welds
One trick method is keeping correct cleanliness in the Visit Website welding area. Extensively cleaning the work surface and surrounding area before welding can aid read what he said minimize these concerns.
An additional ideal method is to thoroughly pick the suitable welding specifications for the certain products being signed up with. This consists of establishing the right voltage, current, travel speed, and shielding gas circulation price. Correct parameter option makes certain optimum weld penetration, combination, and general high quality. Utilizing high-grade welding consumables, such as electrodes and filler metals, can dramatically influence the last weld quality. Buying costs consumables can cause stronger, a lot more durable welds with less flaws. By adhering to these ideal methods, welders can continually produce top quality welds that meet sector requirements and exceed client expectations.
Value of Porosity Control
Porosity control plays an important role in making sure the honesty and high quality of welding joints. Porosity, characterized by the existence of dental caries or spaces within the weld metal, can substantially jeopardize the mechanical properties and structural honesty of the weld. Excessive porosity why not try here weakens the weld, making it extra at risk to cracking, corrosion, and total failing under functional lots.
Efficient porosity control is necessary for keeping the wanted mechanical buildings, such as stamina, ductility, and sturdiness, of the welded joint. What is Porosity. By lessening porosity, welders can improve the total high quality and reliability of the weld, guaranteeing that it fulfills the efficiency demands of the designated application
Additionally, porosity control is important for attaining the wanted visual appearance of the weld. Too much porosity not only compromises the weld yet likewise diminishes its visual appeal, which can be crucial in sectors where appearances are necessary. Appropriate porosity control strategies, such as utilizing the right protecting gas, managing the welding parameters, and guaranteeing proper sanitation of the base products, are essential for producing high-quality welds with minimal defects.
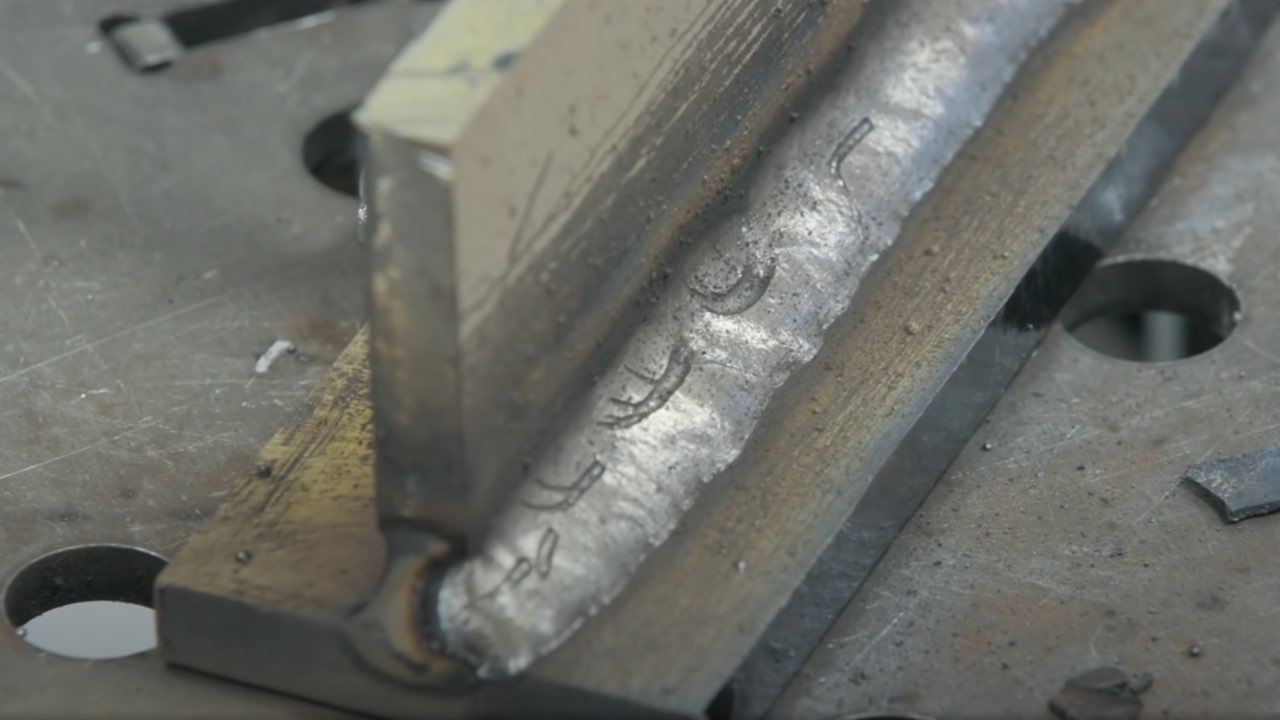
Conclusion
In final thought, porosity in welding is a typical defect that can compromise the top quality of the weld. It is important to manage porosity in welding to guarantee the honesty and stamina of the last product.